Aluminum in the Aerospace Industry
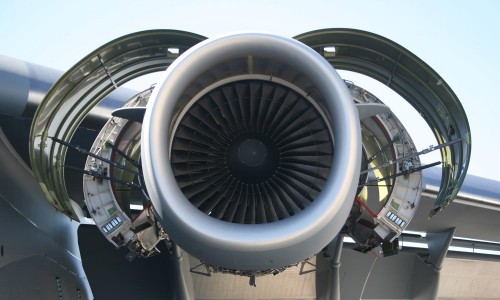
Aluminum is one of the most common metals in the world, with an expansive influence that touches lives every day. From covering dinner in the oven to providing structural elements of an aircraft, aluminum‘s light weight and high strength make it ideal for many applications
A Quick History Lesson
Aluminum has been used in the aerospace industry ever since the Wright brothers built their first plane. Although original plane structures were made of wood, engine crank cases were formed from aluminum and, during World War II, it was so widely used for aircraft manufacturing that civilians were encouraged to donate scrap aluminum to the war effort.
Today, like many industries, aerospace makes wide use of aluminum manufacturing. Due to itsvaluable properties, aluminum has become ideal for lowering costs of aircraft manufacturing while upholding stringent specifications required in the industry.
Aluminum’s Benefits
With a number of beneficial properties, aluminum is an easy choice for manufacturing aircraft. Wood was originally used to build aircraft, but it is prone to rot and can splinter without proper maintenance.
Likewise, steel is stronger than aluminum, but weighs significantly more. Steel is only used in aircraft when extremely high strength is needed, such as landing gears, or extremely high-speed planes.
Some of the benefits of aluminum include:
- Light Weight — The use of aluminum alloys reduces the weight of an aircraft significantly. With a weight roughly a third lighter than steel, it allows an aircraft to either carry more weight, or become more fuel efficient.
- High Strength — Aluminum’s strength allows it to replace heavier metals without the loss of strength associated with other metals, while benefitting from its lighter weight. Additionally, load-bearing structures can take advantage of aluminum’s strength to make aircraft production more reliable and cost-efficient.
- Corrosion Resistance — For an aircraft and its passengers, corrosion can be extremely dangerous. Aluminum is highly resistant to corrosion and chemical environments, making it especially valuable for aircrafts operating in highly corrosive maritime environments.
Aluminum Alloys
There are a number of different types of aluminum, but some are more suited to the aerospace industry than others. Examples of such aluminum include:
- 2024 — The primary alloying element in 2024 aluminum is copper. 2024 aluminum can be used when high strength to weight ratios are required. Like the 6061 alloy, 2024 is used in wing and fuselage structures because of the tension they receive during operation.
- 5052 — The highest strength alloy of the non-heat-treatable grades, 5052 aluminum provides ideal expediency and can be drawn or formed into varying shapes. Additionally, it offers excellent resistance to saltwater corrosion in marine environments
- 6061 — This alloy has good mechanical properties and is easily welded. It is a common alloy for general use and, in aerospace applications, is used for wing and fuselage structures. It is especially common in homebuilt aircraft.
- 6063 – Often referred to as the “architectural alloy,” 6063 aluminum is known for providing exemplary finish characteristics, and is often the most useful alloy for anodizing applications.
- 7050 – A top choice for aerospace applications, alloy 7050 displays much greater corrosion resistance and durability than the 7075. Because it preserves its strength properties in wider sections, 7050 aluminum is able to maintain resistance to fractures and corrosion.
- 7068 – 7068 aluminum alloy is the strongest type of alloy currently available in the commercial market. Lightweight with excellent corrosion resistance, the 7068 is one of the toughest alloys presently accessible.
- 7075 — Zinc is the main alloying element in 7075 aluminum. Its strength is similar to that of many types of steel, and it has good machinability and fatigue strength properties. It was originally used in the Mitsubishi A6M Zero fighter planes during World War II, and is still used in aviation today.
Aluminum has proven highly versatile throughout history, and continues to do so today. The aerospace industry continues to benefit from the alloy’s properties in order to create safer, more reliable and less expensive aircrafts. This will ensure that aluminum will continue to be a valuable material well into the future.